The Sentinel Advantage
Sentinel is the world-leader in the use of High-Density Polyethylene (HDPE) for high performance boat building.
The innovative use of this advanced polymer, combined with cutting-edge design and master craftsmanship derived from Tasmania’s rich maritime history, has resulted in a product that offers unrivalled performance and safety.
Longevity
With exceptional strength and impact resistance, superior durability, zero hull corrosion and no delamination or fibreglass ‘rot’ issues, Sentinel Boats provide significant whole-of-life operational savings over equivalent aluminium, fibreglass or composite hulls.
In demanding daily commercial operations, Sentinel Boats are proven to last over three times longer than equivalent aluminium vessels. This is because HDPE does not suffer from electrolysis or corrosion and can withstand rough impacts. Resistance to marine growth also means the material requires no anti-fouling or painting, both benefiting the environment and resulting in reduced operational costs and minimal maintenance downtime.
Our first workboats, constructed for the Tasmanian aquaculture industry using HDPE, are still in service after nearly 30 years of daily operation in the harsh Southern Ocean. While the outboard engines on some boats have been replaced more than ten times, the HDPE hulls have required only minor maintenance, resulting in exceptional operational availability.
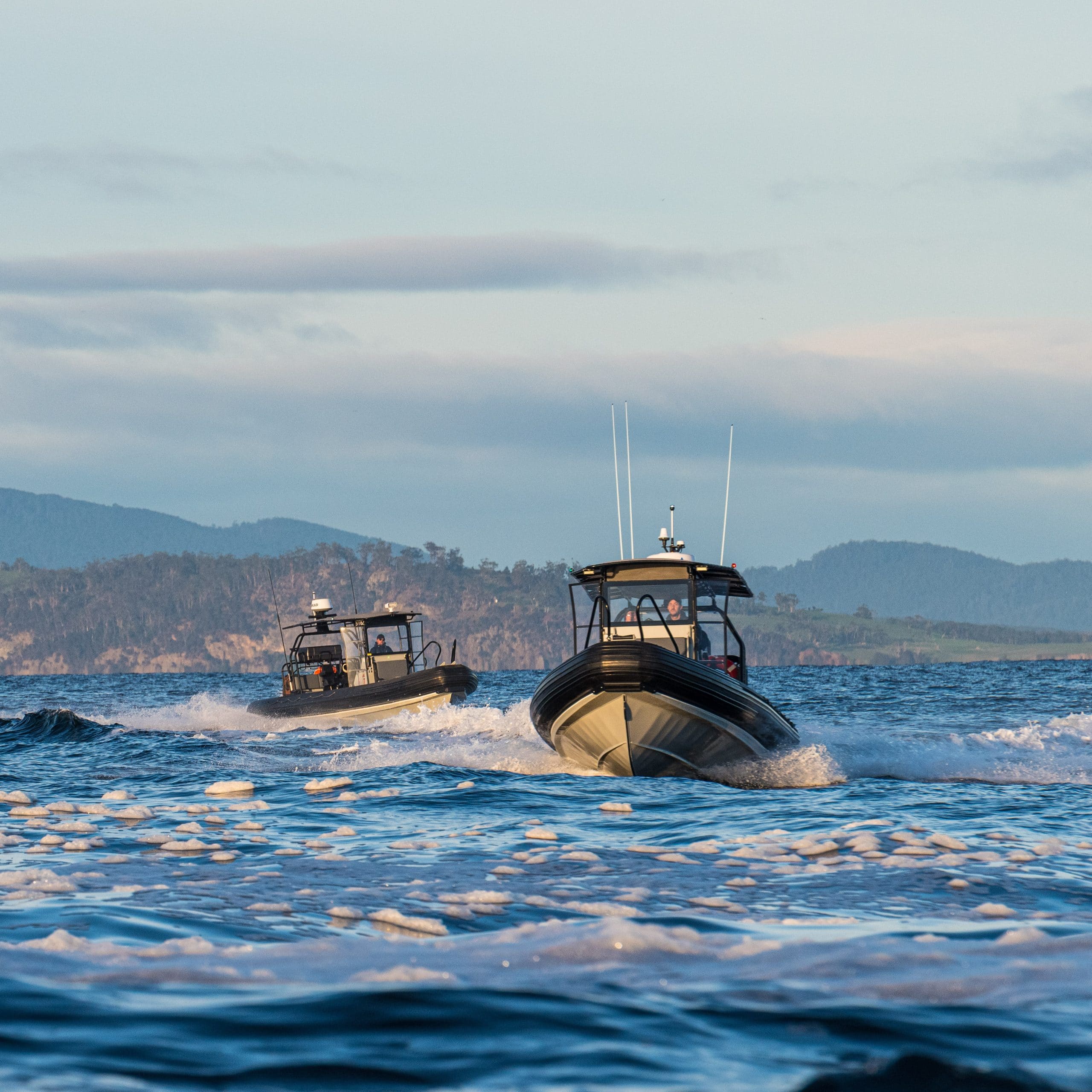
Safety
Our origins in the harsh Southern Ocean have honed our commitment to safety. In tough, high-energy environments, failure is simply not an option: products must withstand the elements to return crews home safely every time.
Sentinel Boats maximise safety through a combination of intelligent design, cutting edge construction methods and the unique material qualities of HDPE.
Our hulls offer industry-leading vibration and shock absorption capabilities, resulting in superior ride and handling characteristics, reduced noise and slamming, especially in adverse conditions. These qualities combine to dramatically reduce personnel fatigue, allowing crews to stay on the water for longer and remain ready to perform their required tasks.
The impact resistance and positive buoyancy of HDPE, combined with the inherent strength provided by our construction methods make our boats virtually indestructible, with the ability to withstand hard beaching, impacts with floating objects and contact with underwater obstacles, common in urban flood or reef/rocky coastal environments. Our specialist Defence vessels can also be customised for air-droppable capability.
Operators have successfully executed hard beaching, high-speed interceptions and rescues off rocky coastlines that would never be attempted in aluminium, fibreglass, or composite vessels.
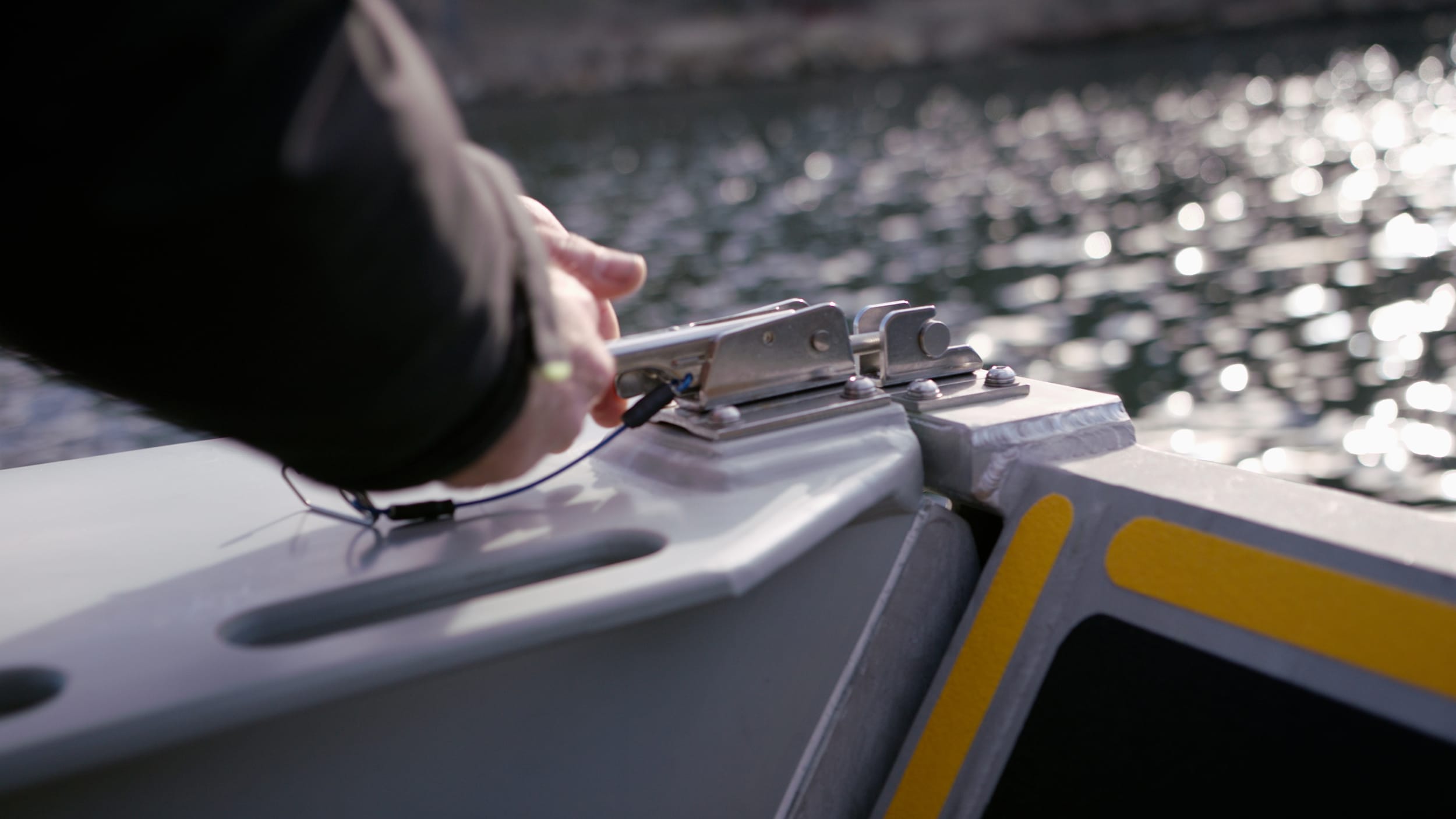
Tailored Performance & Strength
Every Sentinel is hand-built by highly skilled craftspeople using a combination of traditional shipwright techniques and cutting-edge proprietary fabrication methods.
We use full double continuous welding throughout the hull structure, giving our vessels their signature strength and durability. HDPE butt welding results in a homogeneous joint that provides the same strength as the original material, unlike aluminium welds, where the overall strength of the material is reduced. The HDPE fillet, or T welds used across our frames and stringers also provide superior strength over equivalent aluminium welds.
The Sentinel range is highly customisable to suit a range of mission profiles and we work in close partnership with internationally renowned One2Three naval architects. This allows us to optimise performance and respond to even the most challenging design and capability requests. From Norway to New Zealand, and across all states of Australia our boats perform a wide range of roles from survey operations and oil recovery tasks through to protecting our environment and Defence and Law Enforcement deployments,
Our partnership with One2Three naval architects, combined with our on-water experience and the flexible nature of our design and build process, results in our clients taking ownership of a vessel that is tailored to their unique needs and operational requirements.
There is nothing like first-hand experience, honed by the toughest environments on the planet.
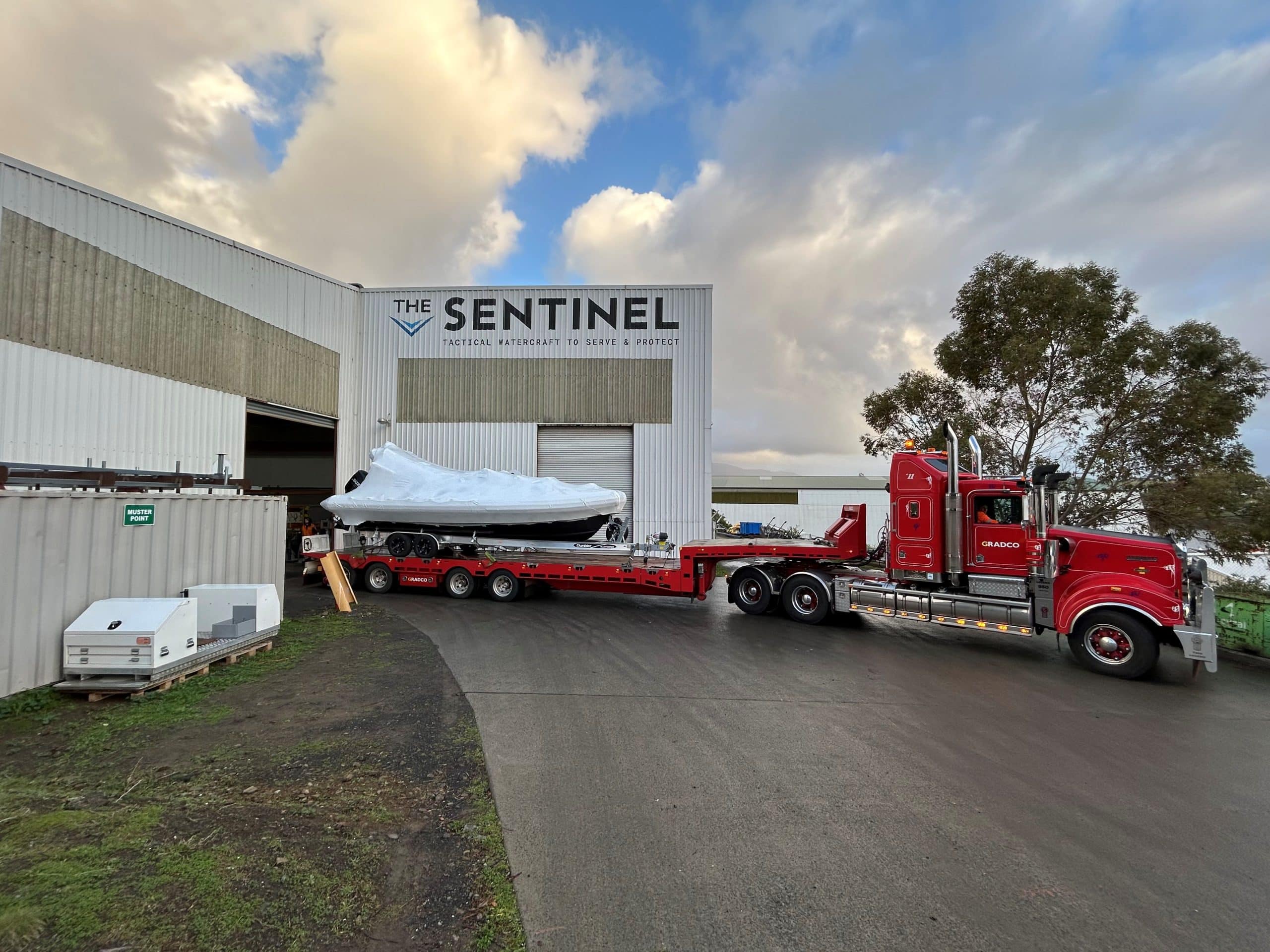
Why HDPE?
Sentinel is a world-leader in the use of High-Density Polyethylene (HDPE) for high performance boat building.
HDPE is a next-generation boat building material that offers superior strength, durability and ride characteristics compared with traditional aluminium, fibreglass, and other composite materials.
The combination of HDPE, cutting edge design and meticulous craftsmanship has resulted in a family of boats that can outperform and outlast anything in their class, resulting in impressive longevity and, importantly, whole of life savings for owners.
As part of our constant efforts to push the boundaries of what is possible using HDPE, Sentinel Boats has carried out extensive independent material testing in partnership with the Australian Maritime College and the University of Tasmania. This has allowed us to combine the lived experience of the durability and longevity of our products with a scientific understanding and rigorous testing data.
The competitive advantage of HDPE is clearly demonstrated when testing impact resistance. Tests designed to simulate a major impact with an obstacle or another vessel caused a breach in aluminium, fiberglass and carbon fibre reenforced fiberglass sheets. Subject to the same force, the watertight integrity of HDPE was maintained, which, in a real-world scenario, would allow the vessel and its passengers to return safely to port to conduct minor repairs.
HDPE, and Sentinel Boat’s unique construction method, honed over 40 years, guarantees superior strength and durability unlike any other boat building material. Combined with advanced design, Sentinel Boats stands alone in the global boat building industry for high performance and user focused tailored small craft solutions.
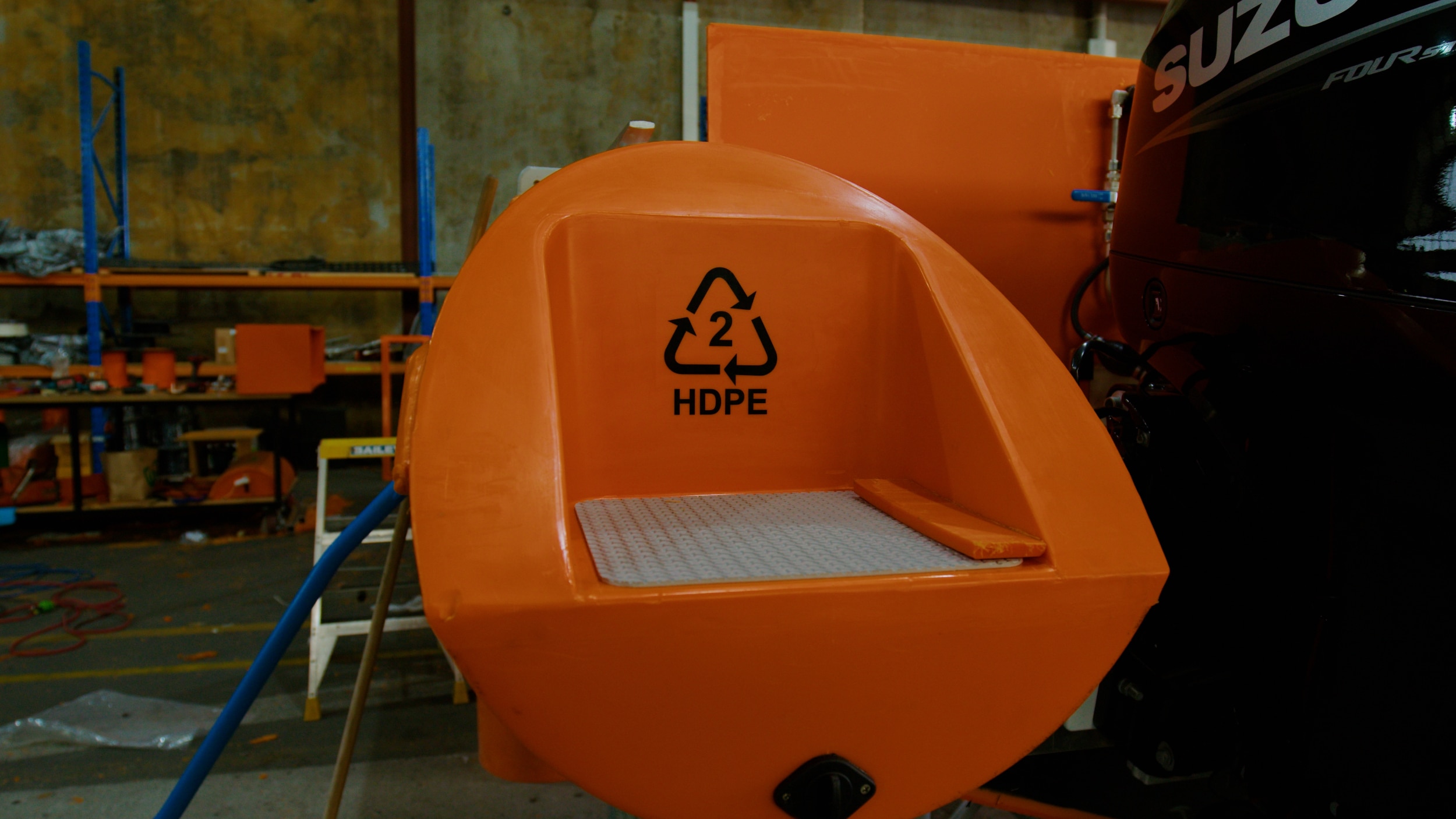
Sustainability
Sentinel Boats has a strong commitment to sustainability which starts with leveraging Tasmania’s renewable energy advantage, meaning our boats are built using 100% renewable energy.
HDPE also provides sustainability advantages over conventional boatbuilding materials. A heavy use operator, such as the aquaculture industry, would expect to replace an aluminium boat after 10 years. We have HDPE boats that are still going strong after nearly 30 years in the water, resulting in significant cost savings for the operator, and avoided emissions from energy and materials that would otherwise be required to manufacture replacement boats.
HDPE uses 20% of the carbon required for aluminium production and is 100% recyclable. All off-cuts from the build process are collected and recycled. At the end of their (very long) life, the material used in the hulls of our boats is also fully recoverable and reusable.
With an occasional high-pressure wash, and a ‘flame’ over the hull every few years HDPE hulls do not require any antifoul treatment, resulting in fewer lift-outs, minimal maintenance and more operational hours. This has the added benefit of reducing the amount of anti-fouling paint in our marine environment.
HDPE is the modern, sustainable and robust choice for applications that demand the very highest standard of performance, durability, safety and operational availability.
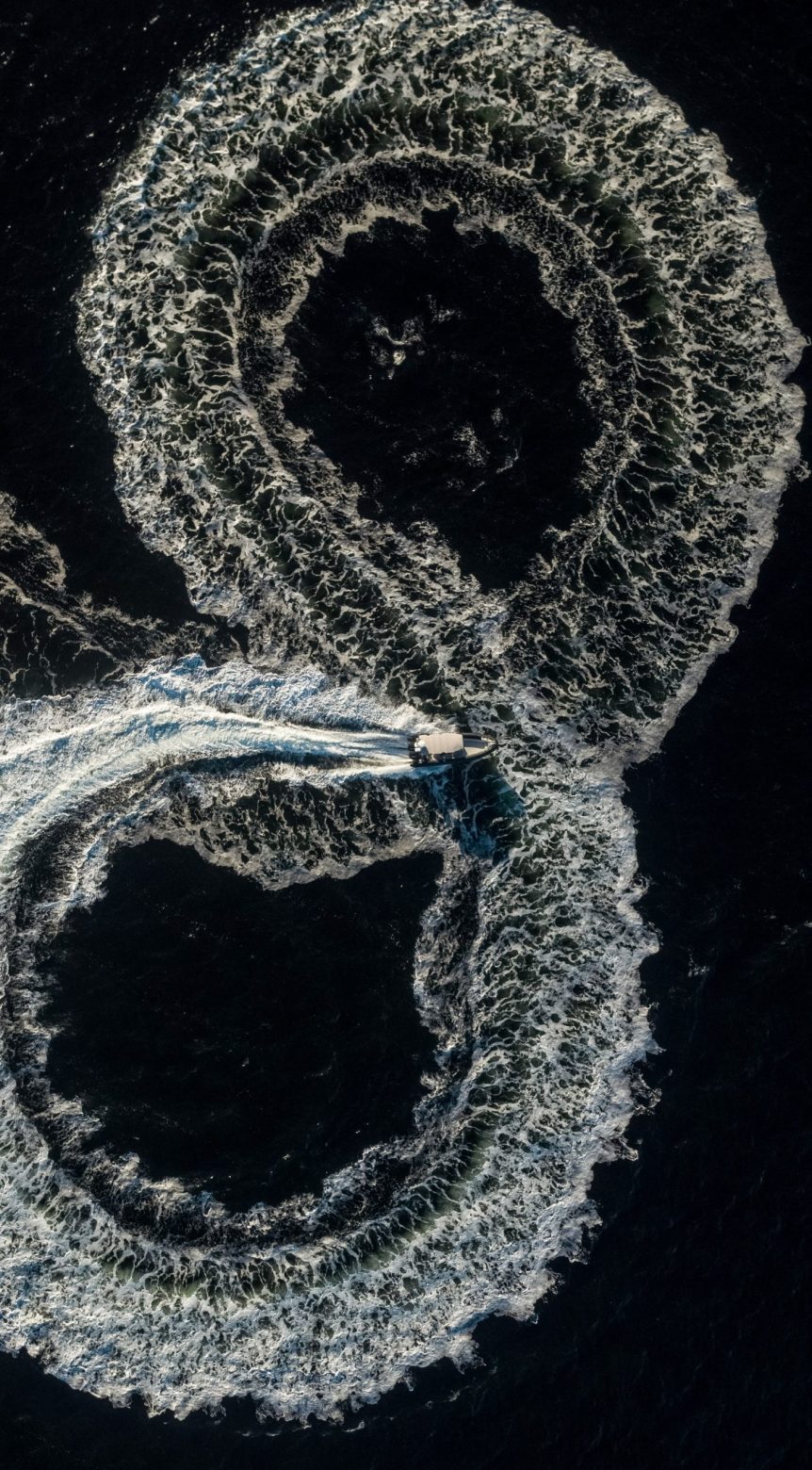
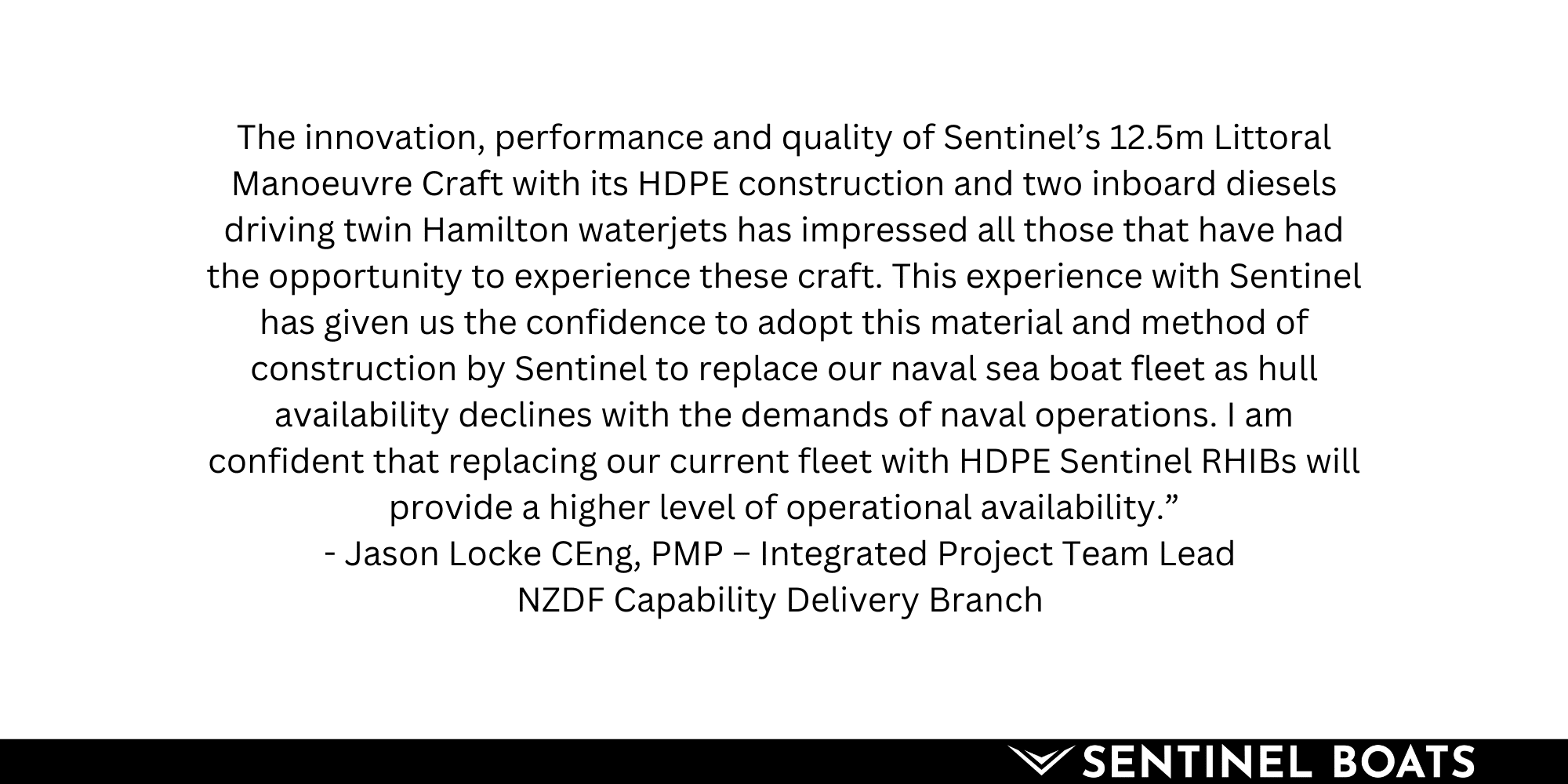
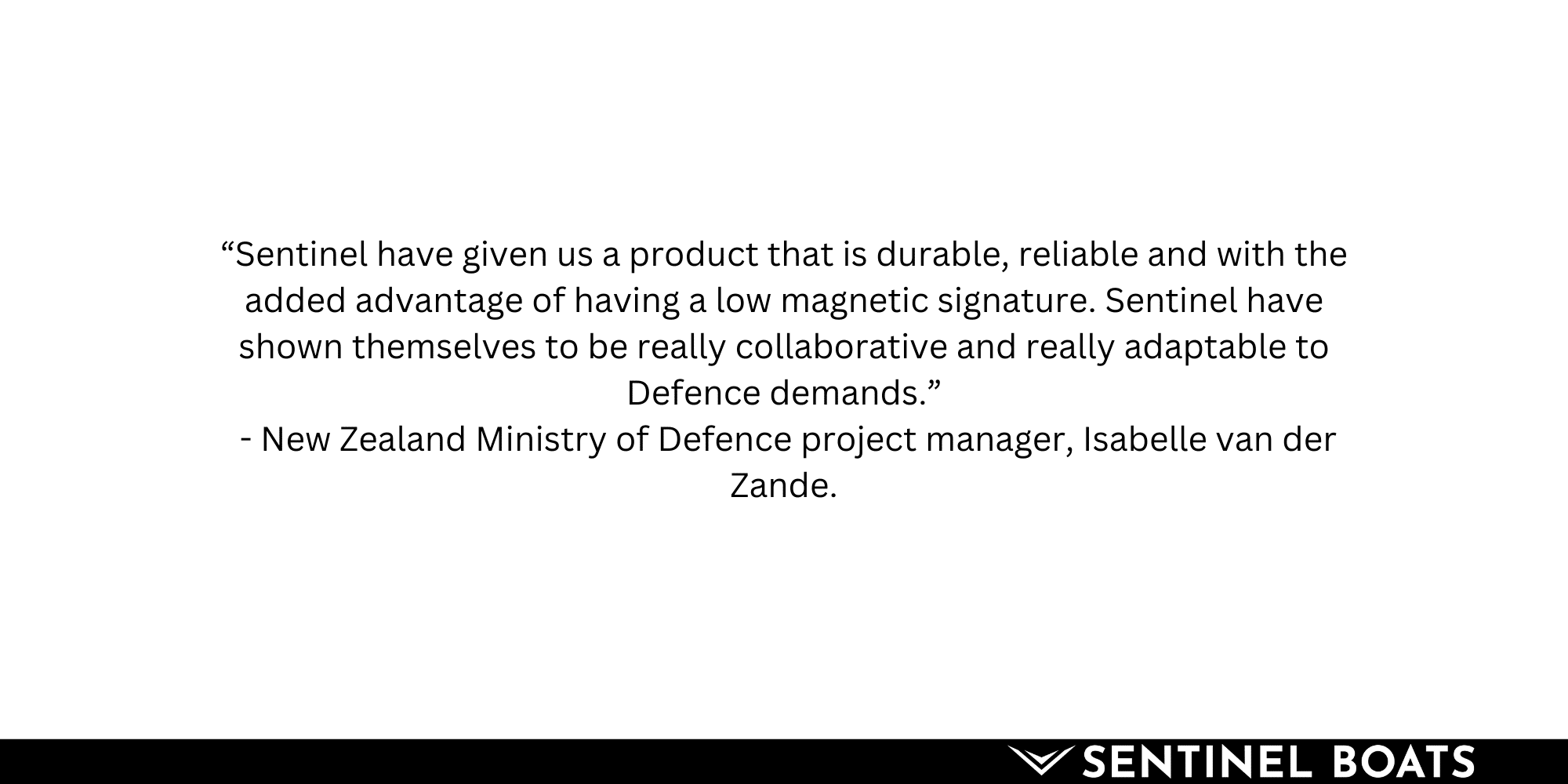
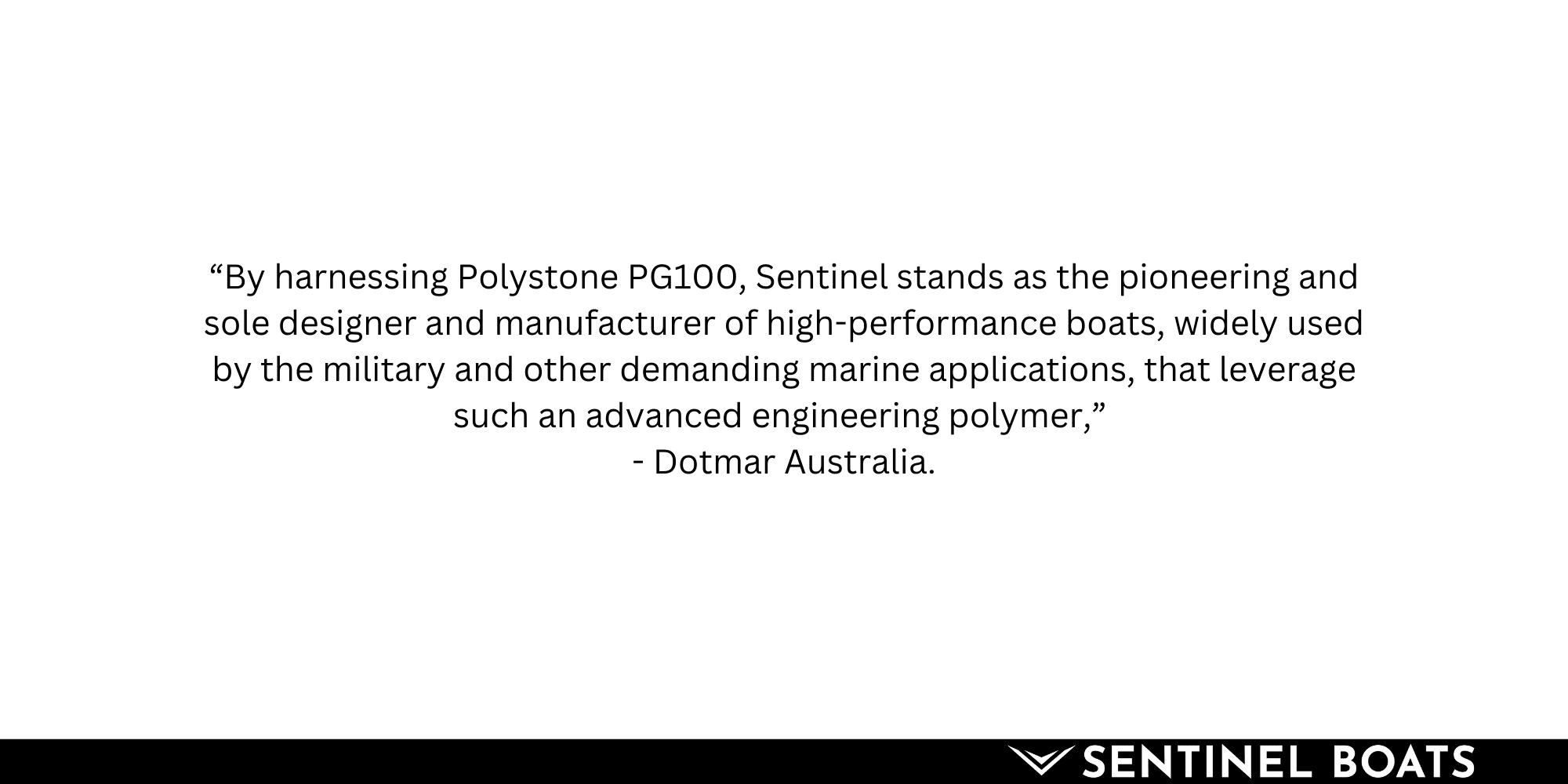
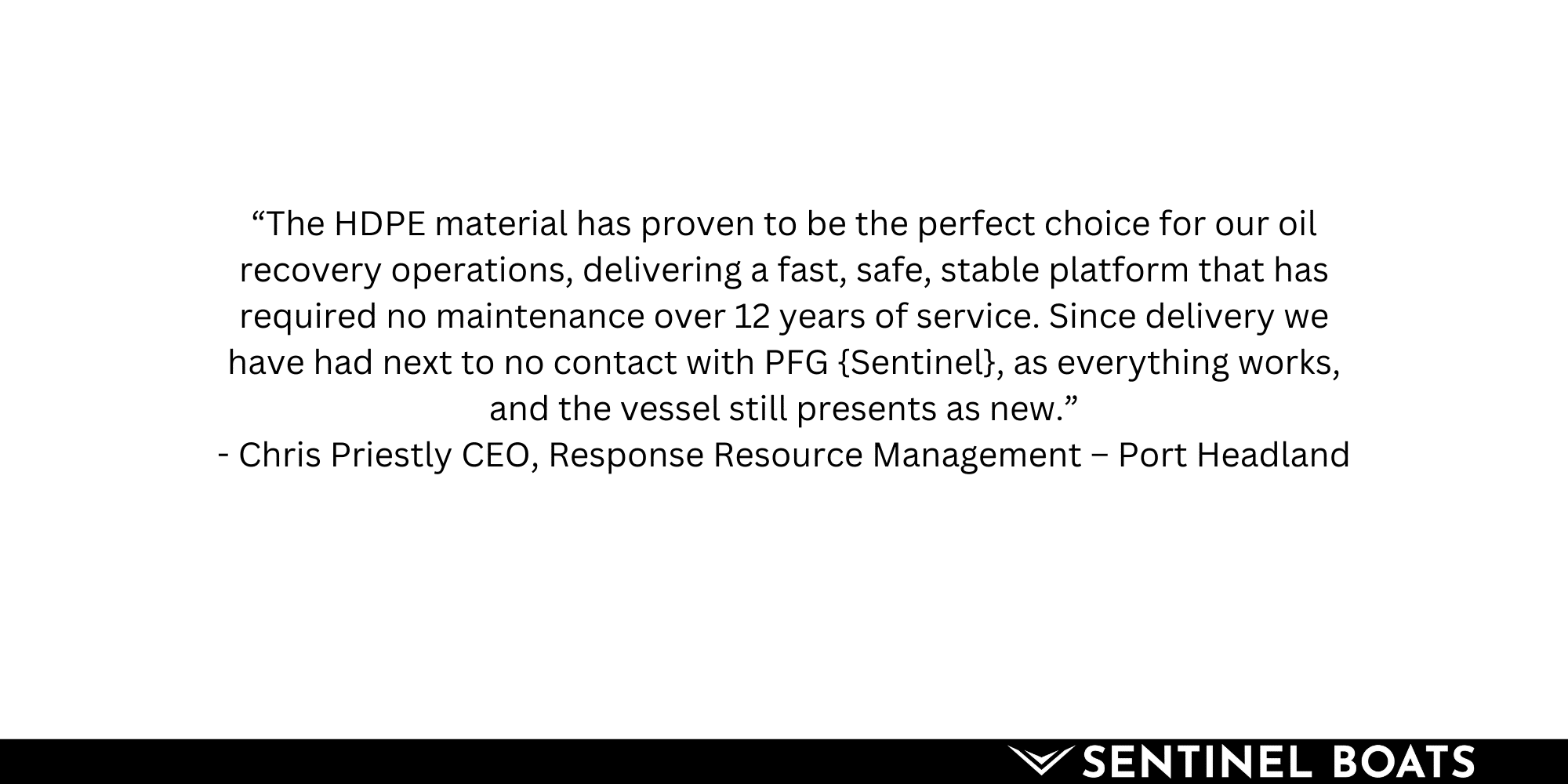
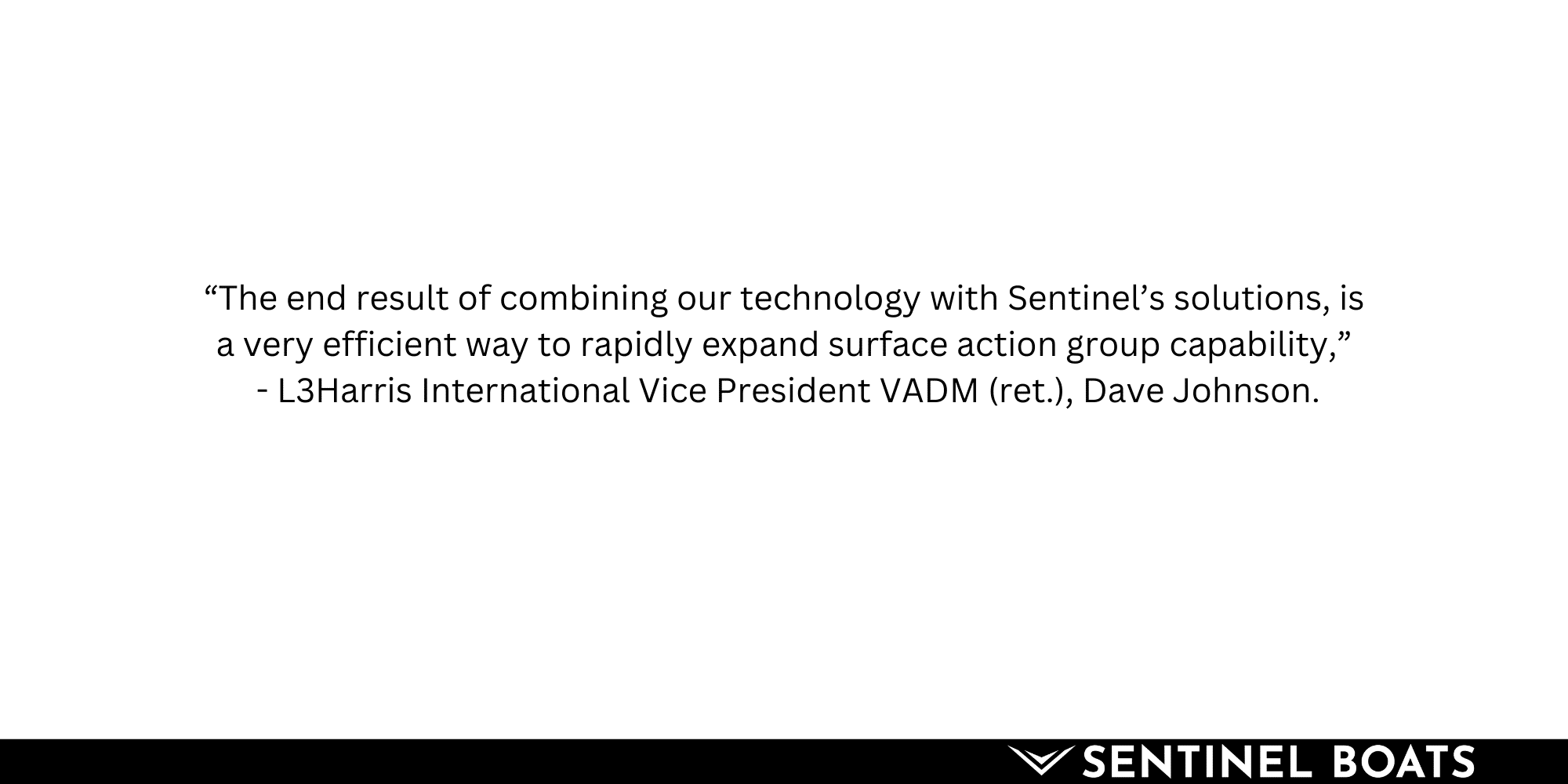
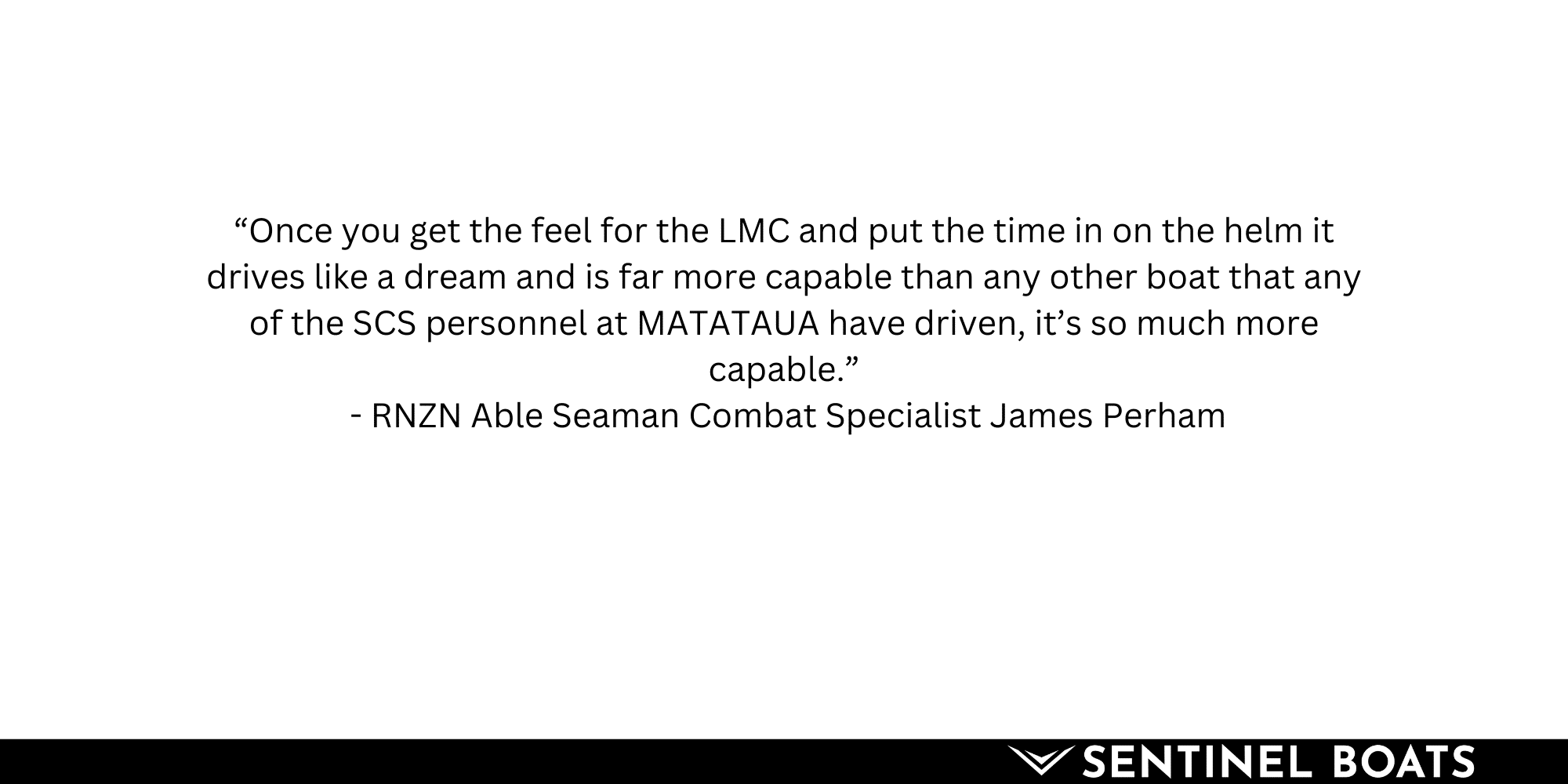
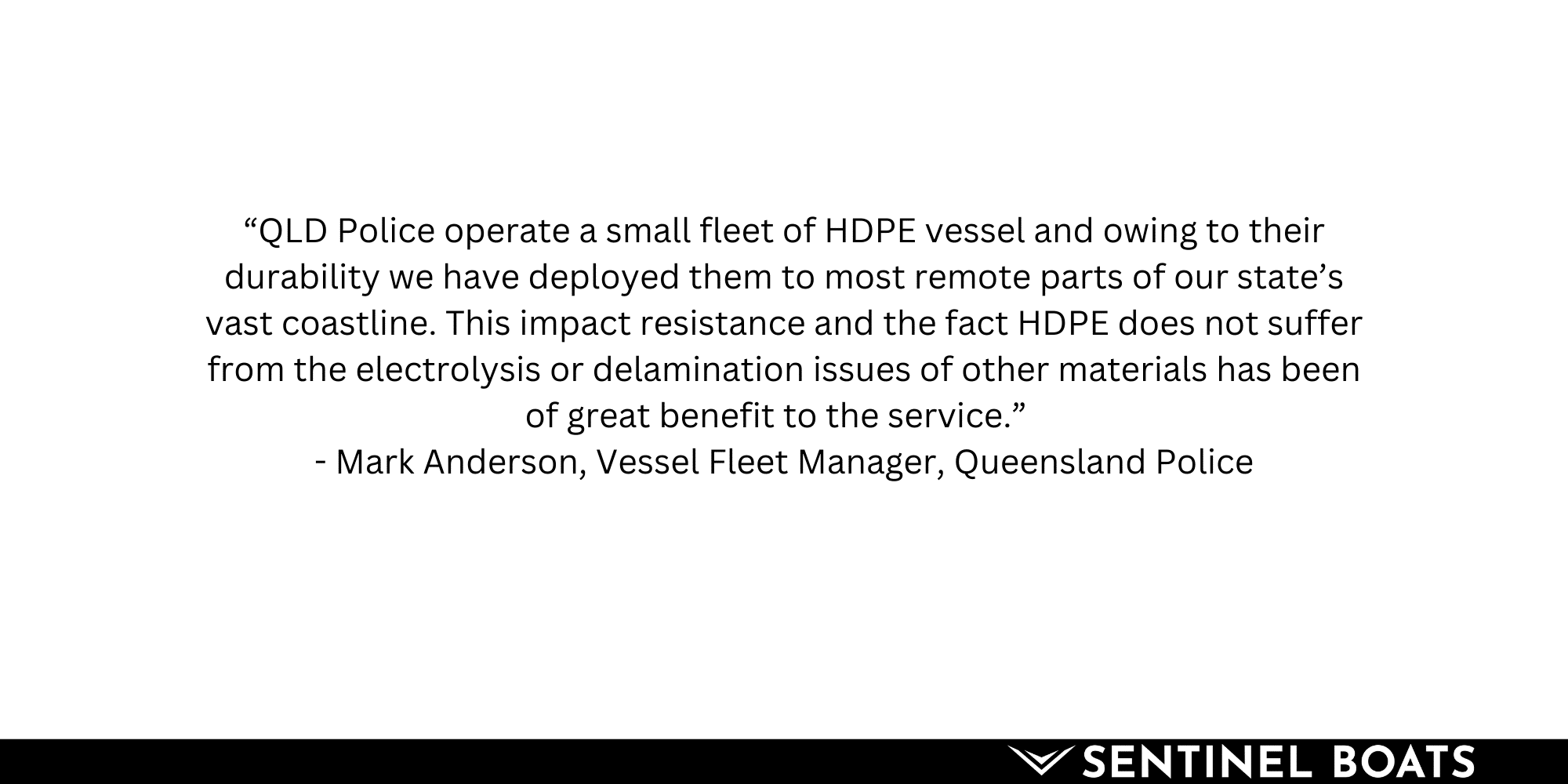